3D PRINTING DFAM
3D PRINTING Options
SLS AND MJF
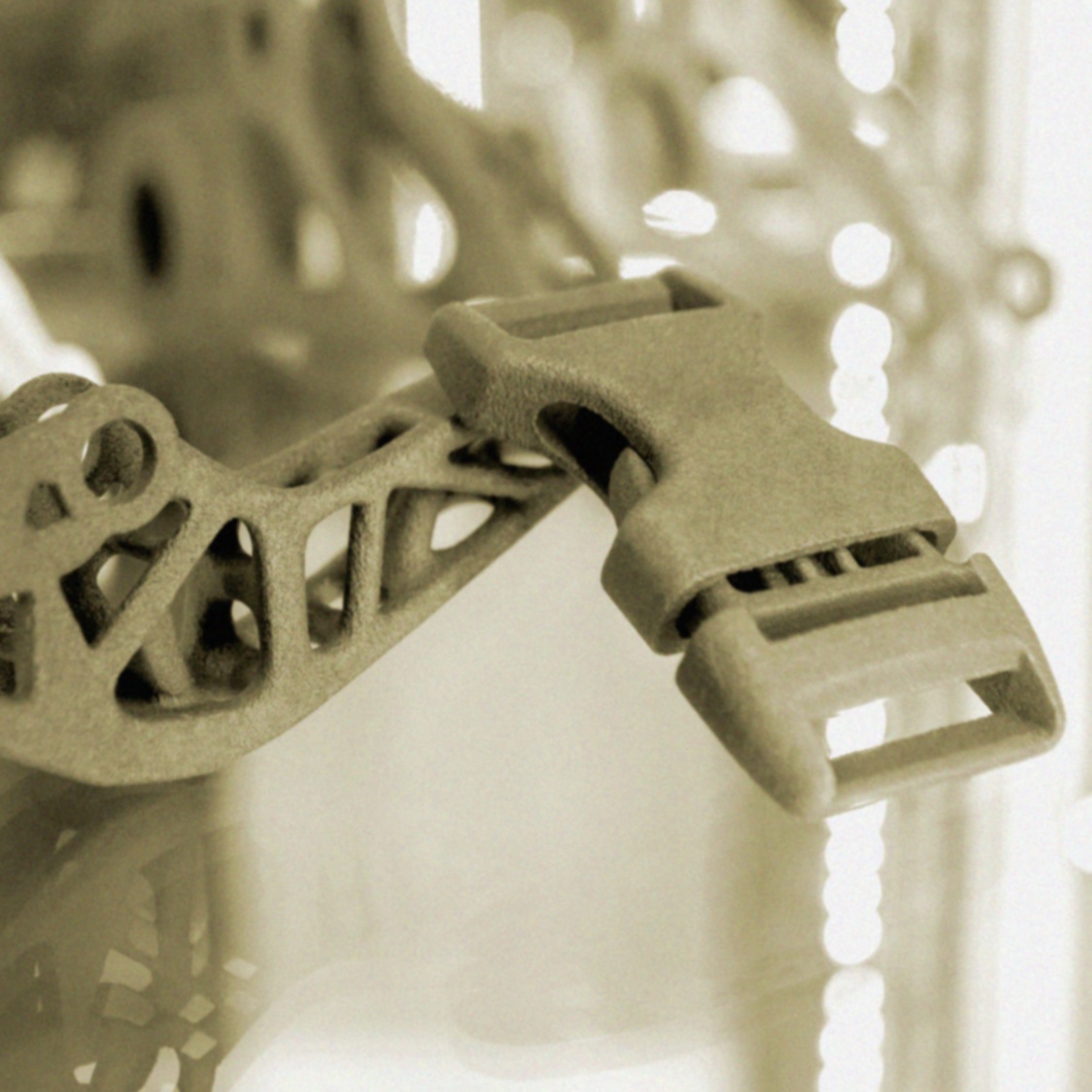
SLS and MJF are not only ideal for prototyping but they also offer a cost effective alternative to injection molding for small batch runs without the hefty upfront cost of tooling. Our powder base technologies help you create high-quality components quickly, allowing you to test your product and scale with confidence.
FDM
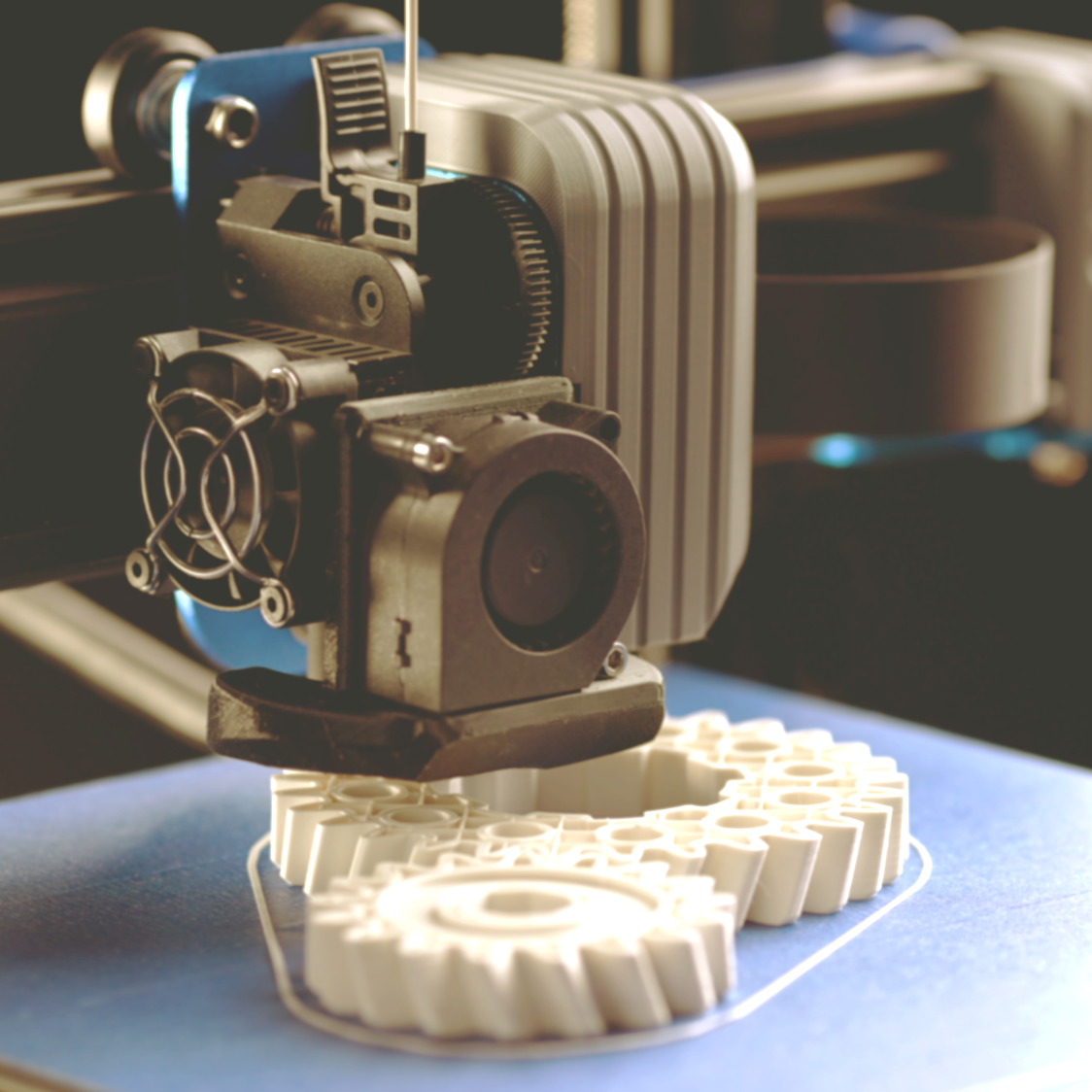
Fused Deposition Modeling is the fan favorite additive method, offering the widest range of material options for everything from functional prototypes to end-use parts. With its large build tray, durable material and proven reliability FDM technology is the perfect fit for many different applications.
SLA
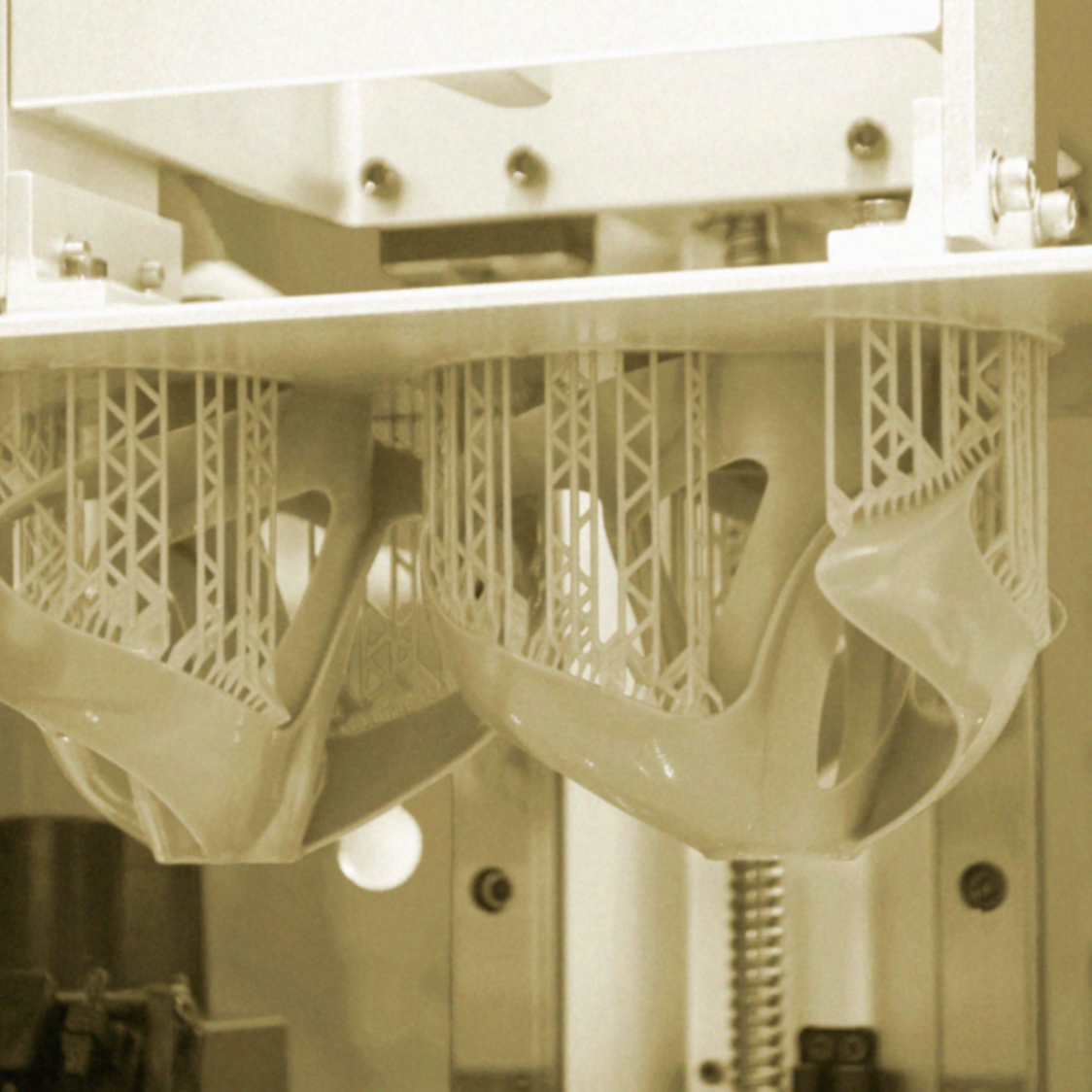
Stereolithography is the OG additive technology known for producing high resolution, tight tolerance prototypes, and smooth detailed production parts. We love using SLA for final design fit checks, quick turn show models, and intricate test fixtures.
TESTIMONIALS
Whether it's additive or subtractive, it's collaborative. See for yourself.
“We reached out to Onit for support on a cost-reduction initiative for one of our overly complex assemblies. The Onit team was instrumental in redesigning several components from metal to plastic, and they even helped consolidate a few part numbers, which streamlined our BOM and ultimately lowered our overall costs."
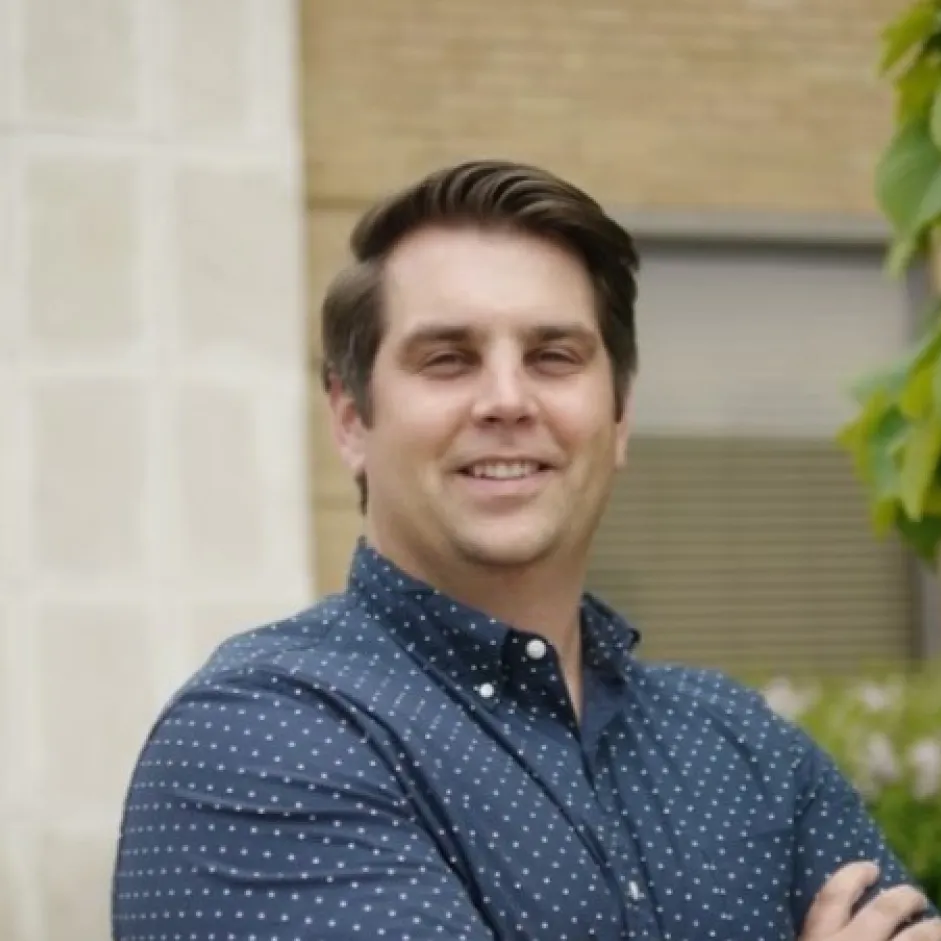
"Onit Mfg has delivered cost-effective, high-quality molds, mold bases and cavities on time and to specification. The craftsmanship and accuracy of the mold-tooling have noticeably improved the quality of Lemo products by increasing yields and reducing cosmetic errors and waste by over 20%."
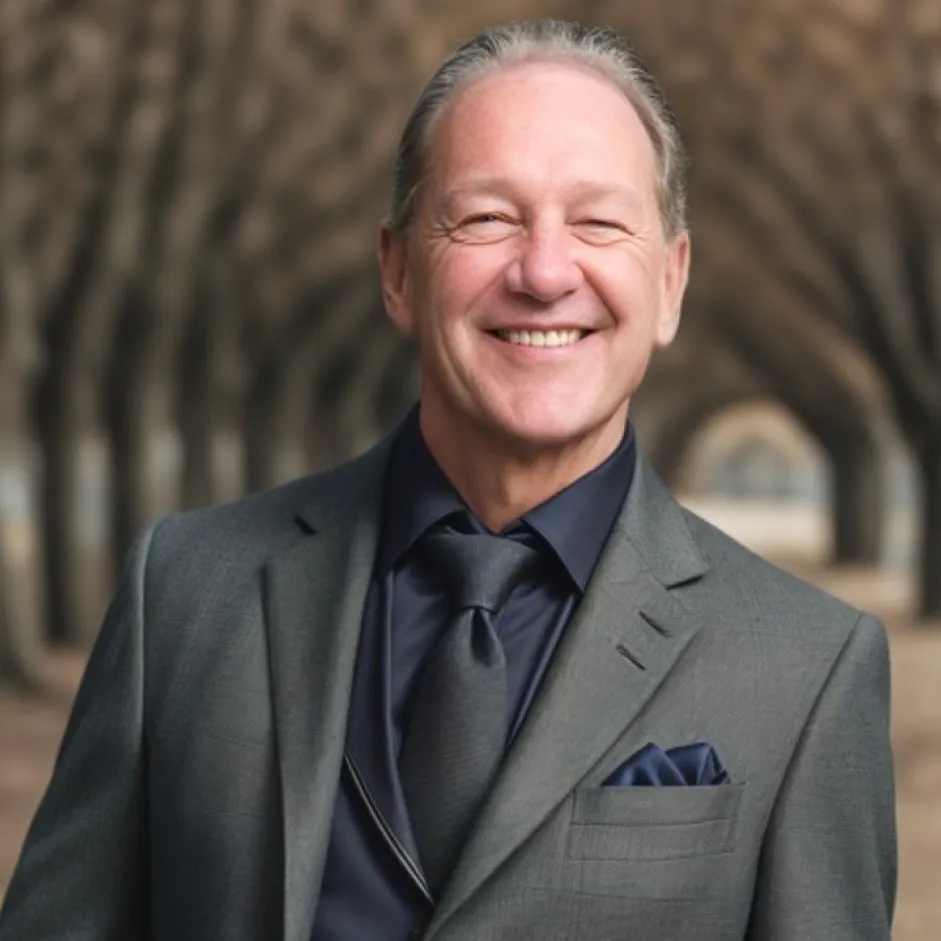
"Onit Mfg has been one of the most communicative and accountable vendors that I've worked with. Where they shine is their excellent communication and customer service, as well as their ability to address complex manufacturing challenges."
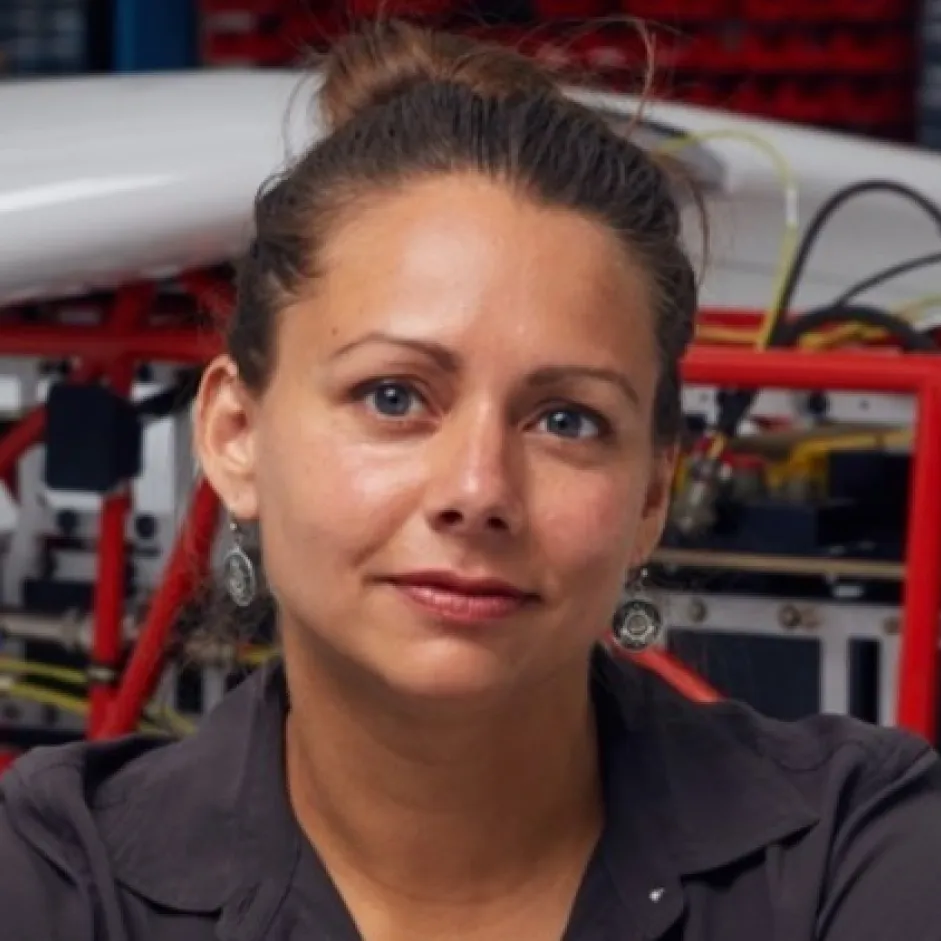